The main preparation processes for magnesium oxide for cover glass are as follows:
1. Magnesium hydroxide method: Using natural dolomite or magnesite as raw materials, magnesium hydroxide is obtained through calcination, digestion, filtration, drying, calcination and other processes, and then high-temperature melting, cooling, crushing, sieving and other processes are used to obtain magnesium hydroxide. magnesium.
2. Magnesium carbonate method: Using natural magnesite as raw material, magnesium oxide is produced through processes such as calcination, carbonization, melting, cooling, crushing, and sieving.
3. Electrolysis method: Using seawater or salt lake water as raw material, magnesium oxide is produced through electrolysis.
Among them, the magnesium hydroxide method is currently the most commonly used magnesium oxide preparation process for cover glass. This process has simple process flow, low equipment investment and low production cost, but the product purity is low and requires secondary refining. The magnesium carbonate method has a more complex process flow, larger equipment investment, and higher production costs, but the product purity is higher. The electrolysis process is more environmentally friendly, but the product purity is low and requires secondary refining.
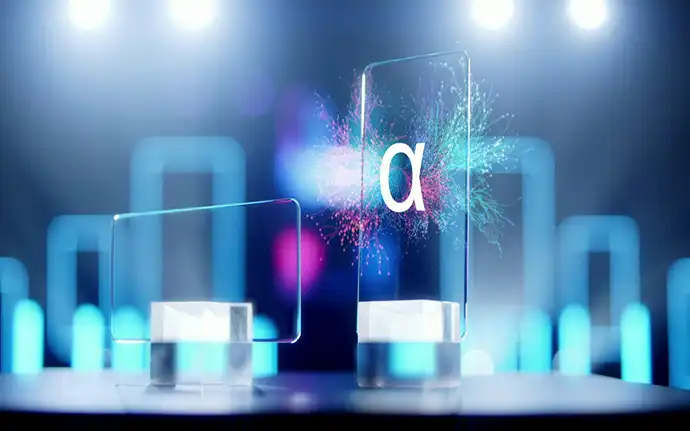
The quality requirements for magnesium oxide used for cover glass are relatively high, including the following:
Purity: The purity of magnesium oxide used for cover glass should not be less than 99.5%.
Particle size: The particle size of magnesium oxide used for cover glass should be controlled between 100-200 mesh.
Water absorption: The water absorption of magnesium oxide used for cover glass should not be higher than 0.5%.
Sinterability: The magnesium oxide used for cover glass should have good sintering properties and should be able to form a good crystal structure.
The main applications of magnesium oxide for cover glass include the following:
As a filler for cover glass, it can improve the strength, hardness, wear resistance and corrosion resistance of cover glass.
As a flux for cover glass, it can lower the melting point of cover glass and improve the fluidity of cover glass.
As a crystal nucleating agent for cover glass, it can promote the crystallization of cover glass and improve the strength and hardness of cover glass.
As the application fields of cover glass continue to expand, the demand for magnesium oxide for cover glass will also continue to increase.