In 1994, the cellulose diacetate production line of Nantong Company was put into operation, and cellulose diacetate was localized for the first time. Subsequently, Nantong Company has undergone expansions one after another, and its annual production capacity of cellulose acetate has reached 200,000 tons, ranking second in the world in terms of production scale. Over the years, many companies have successively built and put into production cellulose acetate production lines, and the domestic annual production capacity of cellulose acetate has reached 290,000 tons. Therefore, based on the amount of magnesium oxide used in the production of cellulose acetate, the demand for high-purity magnesium oxide in domestic cellulose acetate production exceeds 8,000 tons per year.
In the early days, domestic cellulose acetate production mainly used imported high-purity magnesium oxide from foreign companies, and then gradually replaced it with high-purity magnesium oxide from magnesite in Northeast China. In 2017, with the strengthening of environmental protection, the mining of magnesite in Northeast China was prohibited due to dust pollution and other reasons, and domestic cellulose acetate manufacturers began to use domestic brine-based magnesium oxide. From the perspective of usage, the production of cellulose acetate requires brine-processed magnesia to meet the following quality requirements.
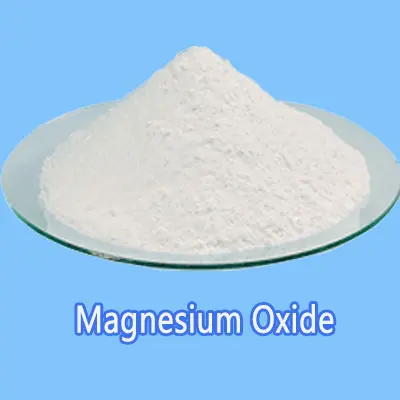
(1) High reactivity and fast reaction temperature rise.
The main use of magnesium oxide is to prepare magnesium acetate solution. This requires magnesium oxide to have high reactivity, fast reaction speed in acetic acid solution, fast reaction temperature rise, and rapid completion of the reaction. In the process of magnesium oxide production, the calcination temperature should be reasonably controlled to prevent dead burning from affecting the reactivity.
(2) The magnesium oxide content is not less than 99.4%.
The content of magnesium oxide is high, and the impurity is few, and the reaction activity is correspondingly improved, and the impurity after reaction is few, and is beneficial to the filtration of magnesium acetate solution, and avoids that impurity is brought into cellulose acetate, affects product quality. The production of cellulose acetate places high purity requirements on magnesium oxide.
(3) Calcium content (calculated as CaO) is not more than 0.3%.
The purpose of controlling calcium content under the premise of high purity is still to further control impurities.
(4) The particle size is not less than 96 mesh.
To control the particle size, one is to prevent the fine particle size of magnesium oxide from producing a large amount of dust during the feeding process and adhering to the wall of the vent pipe, etc., causing pollution or failure; the other is to worry about the fine particle size causing magnesium oxide powder to float on the acetic acid solution block, resulting in uneven reaction and affecting filtration, etc.
(5) Iron content (calculated as Fe2O3) is not more than 0.08%.
The production of cellulose acetate requires high whiteness of cellulose acetate, so it is required to reduce the ingredients in the raw and auxiliary materials that affect the whiteness of the product as much as possible. The iron content index is the key concern index.
(6) The alkalinity is not less than 98%.
Generally, after the purity of magnesium oxide meets the requirements, the alkalinity exceeds 98%.
(7) The bulk density is not less than 0.65g/cm3.
The requirement for the bulk density is mainly to avoid that the light and fine magnesium oxide powder cannot be smoothly added to the acetic acid solution, which will affect the reaction process and bring troubles to the filtration process.
(8) Chloride ion content is not more than 0.02%.
The equipment in the production of cellulose acetate is made of stainless steel. High chloride ions will aggravate the corrosion of the equipment. The chloride ion content of various raw and auxiliary materials is strictly controlled during production.
(9) Acid insoluble matter is not more than 0.2%.
The main reason is to further reduce impurities. During the production of magnesia, attention should be paid to controlling dust pollution. Usually, the content of vinegar insolubles is extremely low.
Hebei Messi Biology Co., Ltd. stated that the production of cellulose acetate has stricter requirements for high-purity magnesium oxide than HG/T2573-2012 “Industrial Light Magnesium Oxide” and the technical indicators are also higher than this standard. This is due to the actual production of cellulose acetate. When developing high-purity magnesium oxide products for the production of cellulose acetate, these indicators should be highly valued, and efforts should be made to study and improve the production process of magnesium oxide to meet the requirements of the indicators.