At present, the raw materials for preparing silicon steel grade magnesium oxide mainly include magnesite (MgCO3), dolomite (CaCO3 MgCO3), magnesium-containing industrial by-products, seawater or salt lake brine (MgCL2), etc. The production process can be divided into basic magnesium carbonate Magnesium ore carbonization method and ammonium bicarbonate method as intermediate, brine pyrolysis method with basic magnesium chloride as intermediate.
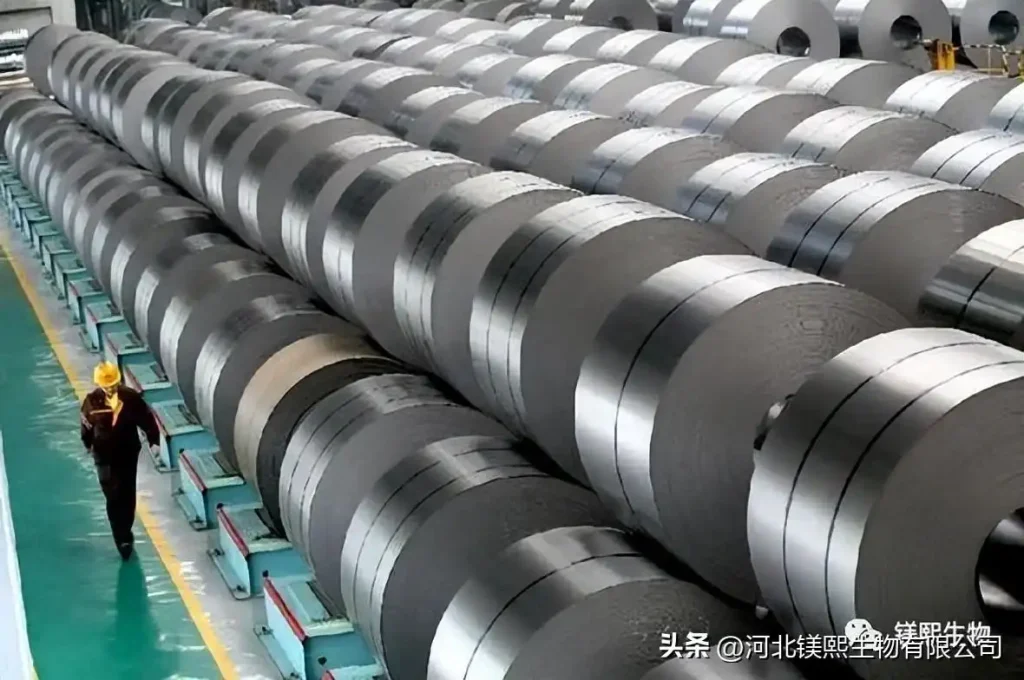
1. Preparation of silicon steel grade magnesium oxide from salt lake brine
Bischofite (MgCL2 6H2O) is dissolved and filtered to remove solid suspended impurities to obtain brine, which is reacted with ammonia to prepare intermediate magnesium hydroxide: MgCL2+2NH3+2H2O=Mg(0H)2+2NH4CL
Magnesium hydroxide is calcined at high temperature to obtain magnesium oxide: Mg(OH)2=Mg0+H2O
2. Preparation of silicon steel grade magnesium oxide by carbonization of magnesium ore
The magnesium ore carbonization method (dolomite, magnesite, etc.) is calcined at high temperature, and the calcined magnesium oxide is hydrated, carbonized, and filtered to achieve the purpose of completely separating magnesium from impurities, and the magnesium-containing filtrate is then pyrolyzed to generate alkali Formula magnesium carbonate precipitates, the precipitate is filtered and calcined, and finally the magnesium oxide product is obtained. The process flow is shown in Figure 1 and Figure 2.
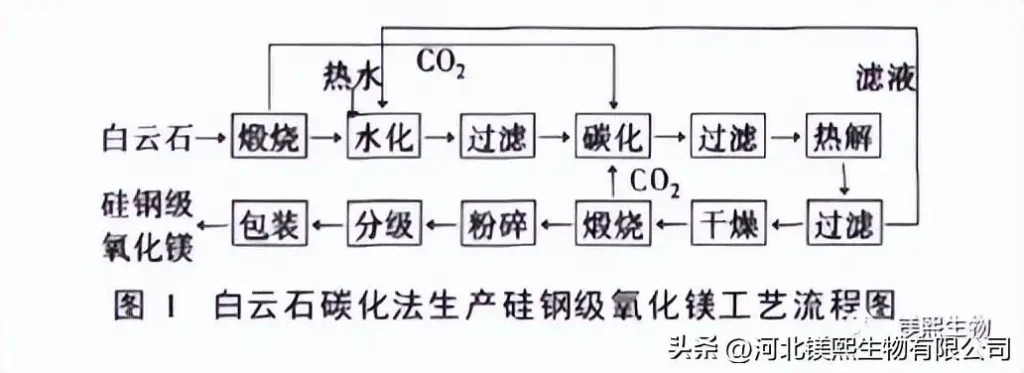
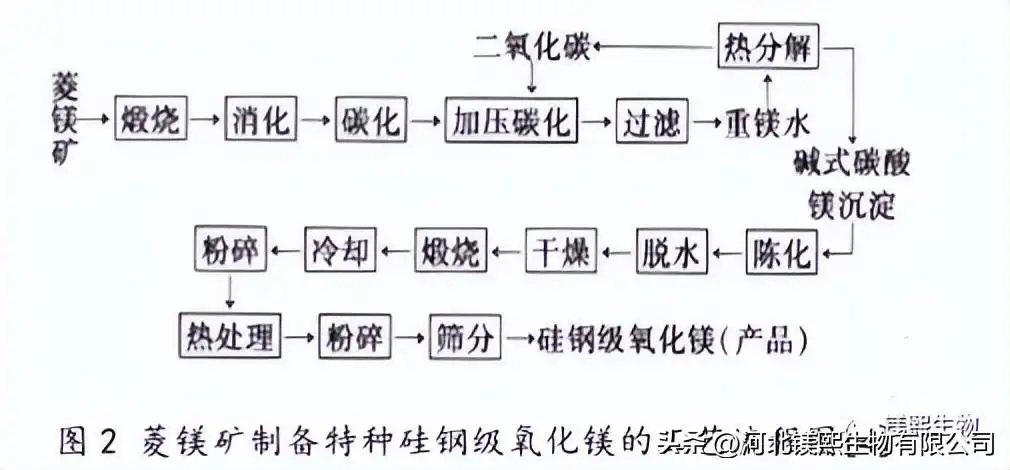
Using hydromagnesite [3MgCO3·Mg(OH)2·3H2O] as raw material, silicon steel grade magnesium oxide was prepared by carbonization method. Put the raw materials into a tubular resistance furnace, calcinate at 750°C for 1.5h, add 1L of water to each 50g of calcined material at 90°C for hydration reaction for 1h, and then inject CO2 into the filtrate at 40°C, and the partial pressure of CO2 is 04~ Carry out the carbonization reaction under the condition of 0.6MPa and end point DH of 7. The carbonized liquid is filtered. The filtrate was pyrolyzed at 90°C to form a basic magnesium carbonate precipitate, which was then filtered and dried, then put into a tubular resistance furnace and calcined at 900°C for 1 hour to finally obtain a hydration rate of <4% (mass fraction) and a suspension of 6mm/h silicon steel grade magnesium oxide. It was found that the hydration rate and apparent specific volume decreased with the increase of basic magnesium carbonate calcination temperature (800~1000°C), and the suspension increased with the increase of temperature.
Dolomite and anthracite are calcined in a high-temperature resistance furnace, and the calcined product is digested with water, filtered by a combined method of coarse sieve-two-stage cyclone separation-vacuum sieve filtration, and the filtrate is carbonized. The concentration of MgO in the carbonized liquid is 26~ 30g/L, the mass concentration of CaO is 42-45g/L, the filtered heavy magnesium aqueous solution is converted into basic magnesium carbonate precipitate through pyrolysis, and then aged, washed, centrifugally dehydrated and dried, and then heated at 950~980℃ Calcined into magnesium oxide, silicon steel grade magnesium oxide with a particle size of ≤3um, a hydration rate of 3.2% (mass fraction), and various indicators better than the enterprise standard was obtained.
Studies have shown that if the pyrolysis temperature is higher than 85°C, the product particles will increase significantly; if the pyrolysis temperature is lower than 55°C, the decomposition will be incomplete in the decomposer, resulting in a decrease in yield. Using ore as raw material to prepare silicon steel grade magnesia by magnesium ore carbonization method, affected by impurities such as calcium in the raw material, the purity of the product is difficult to reach the standard, and at the same time, there are still disadvantages such as high energy consumption and high production cost. Although low temperature pyrolysis Technology has made some breakthroughs in reducing energy consumption, but the product purity of this method is difficult to reach the standard, and it has not been applied to industrial production.
3. Preparation of silicon steel grade magnesium oxide by ammonium bicarbonate method
The ammonium carbonate method is to heat and react ammonium carbonate, ammonium bicarbonate and other precipitants with refined magnesium-containing solutions in a reactor to generate basic magnesium carbonate intermediates. The feed liquid is filtered, washed, dried, calcined, and heat-treated. Obtain magnesia product, technological process is shown in Fig. 3
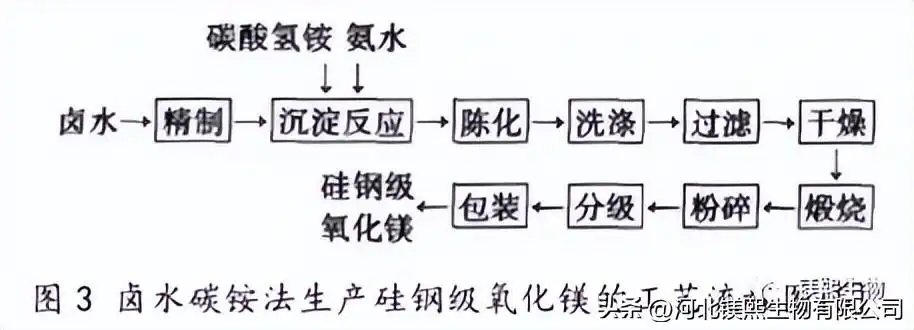
4. Preparation of silicon steel grade magnesium oxide by brine pyrolysis
The brine pyrolysis method is to purify the raw materials through physical and chemical methods, then pyrolyze the purified liquid in air or hot air, gradually lose crystal water, and finally calcinate to obtain magnesium oxide and hydrochloric acid. The process flow is shown in Figure 4.
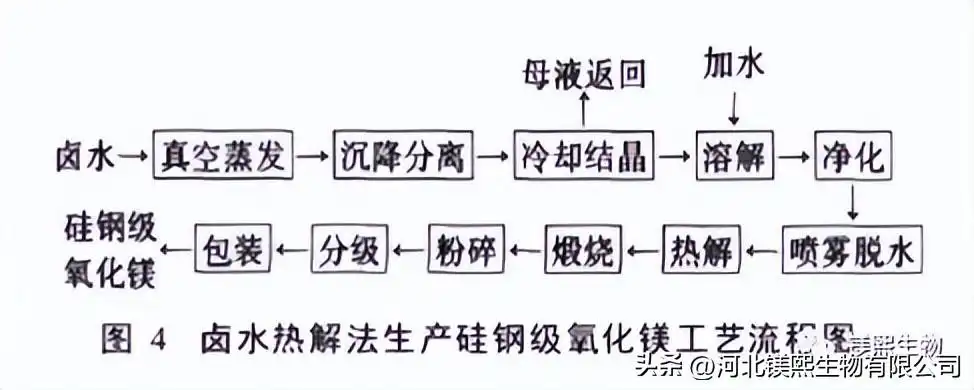