The preparation method of the composite magnesium oxide powder for dental alginate impression material comprises the following specific steps:
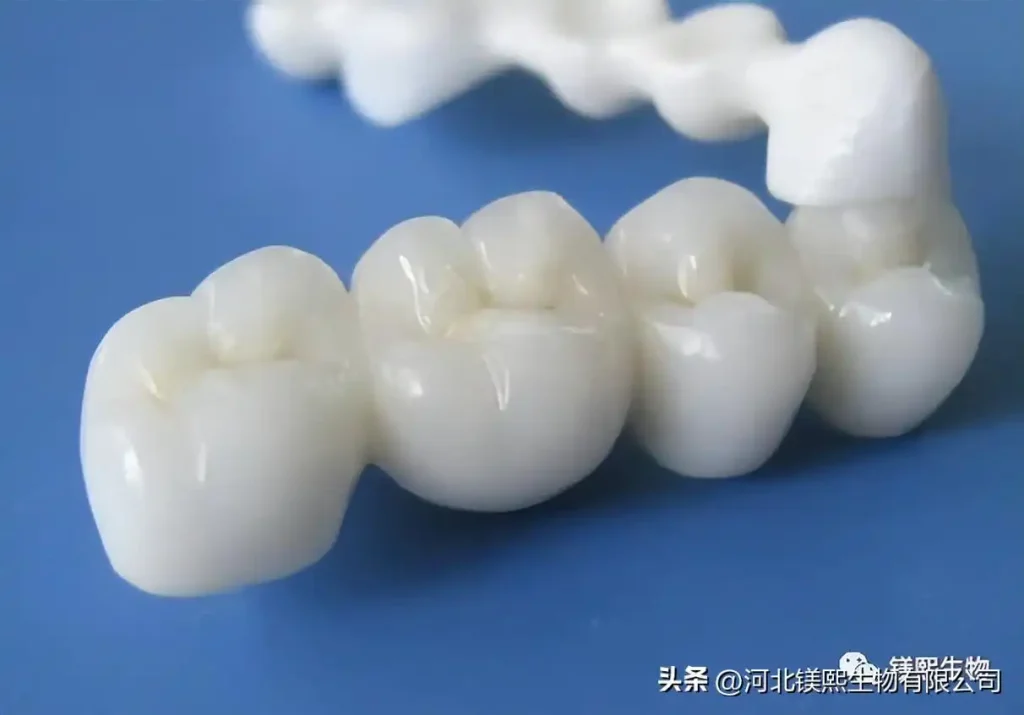
a. Choose magnesium hydroxide powder raw material, magnesium hydroxide content is 97.3%, CaO is 1.3%, SO4 is 0.3%, Cl is 0.10%, heavy metal is 9ppm, As is 3ppm, acid insoluble matter is 0.08%; The weight loss is 31%, the laser particle size D50 is 1.8μm, and the whiteness is 96.
b. Put the raw material magnesium hydroxide powder into the rotary kiln calciner, control the temperature range from the front part to the rear part in the rotary kiln to be 575°C to 625°C, and control the residence time of the material in the calciner to 1.5h. The magnesia powder is passed through a vibrating sieve to obtain a magnesia powder product a of 325 meshes. The range of citric acid value of the reactivity of magnesium oxide a by chemical detection is 136s, the bulk density is 0.31g/cm3, and the whiteness of ginseng is 94. Obtain bagged magnesium oxide powder product a through packaging;
c. choose light magnesium carbonate powder raw material, wherein magnesium oxide content is 43.5%, CaO content is 0.07%, SO It is 0.035%, Cl is 0.03%, heavy metal is 6ppm, As is 3ppm, acid insoluble matter is 0.045%, The weight loss on ignition is 53.5%, the laser particle size D50 is 1.7μm, and the whiteness of ginseng is 95;
d. Add the light magnesium carbonate powder raw material into the rotary kiln calciner, control the temperature range from the front part to the rear part in the rotary kiln to be 900°C to 1050°C, and control the residence time of the material in the calciner to 1.8h . The calcined magnesium oxide powder was passed through a vibrating sieve to obtain a 325-mesh fully-passed magnesium oxide powder product b. The reactivity citric acid value range of chemical detection magnesium oxide a is 76s, the bulk density is 0.15g/cm3, and the whiteness of ginseng is 94, and the bagged magnesium oxide powder product b is obtained through packaging;
e. When performing dental alginate impression material batching, open the bagged magnesia powder product a and the bagged magnesia powder product b, and follow the steps of magnesia powder product a and magnesia powder The weight ratio of body product b is 2.0-0.5:1.0 for mixing to obtain a dental alginate impression material with an activity value of 120s-85s, that is, a composite magnesium oxide powder product. The solidification time is an important parameter of the impression material. The length of the solidification time of the impression material depends on the reactivity of the reactants in the impression material, especially the reactivity of magnesium oxide. The higher the reactivity of magnesium oxide, the faster the solidification of the impression material. The shorter the time.
The composite magnesia powder is a ready-to-use powder obtained by mixing two magnesia powders with different qualities. Among them, the magnesia powder product a obtained by calcining the raw material magnesium hydroxide has low activity, and its The solidification time will be longer; the magnesium oxide powder product b obtained by calcining the raw material light magnesium carbonate has higher activity, and its solidification time will be shorter when it is simply used. In use, according to the solidification time of the impression material, by changing the different ratios of the magnesium oxide powder product a and the magnesium oxide powder product b, the ready-to-use magnesium oxide powder with the required solidification time can be obtained . At the same time, the bulk densities of the two are also different, and ready-to-use composite magnesium oxide powder c with different bulk densities can also be obtained through different proportions.
The composite magnesium oxide powder used for the dental alginate impression material of the present invention has the following outstanding advantages:
(1) Composite magnesium oxide powder makes the target solidification time of dental alginate impression material more accurate;
(2) The uniform compounding of two kinds of magnesium oxide powders increases the success rate of impression material molding;
(3) After the impression material obtained from this product is formed, the impression is complete, clear, smooth and clean, and easy to remove from the mold.