Hebei Messi Biology Co., Ltd. stated that in industrial production, due to the use of different raw materials, there are usually four methods for producing light magnesium carbonate:
The first is the dolomite carbonization method, that is, dolomite or magnesite is calcined together with coal, and the clinker obtained after calcination is sent to the digester to be digested with waste magnesium water into a gray emulsion of a certain concentration, and the gray emulsion is sent to the It enters the carbonization tower and reacts with carbon dioxide in the cleaned and pressurized kiln gas from the calcination kiln. The carbonized slurry after carbonization is separated and filtered to obtain filter residue and clear filtrate, that is, magnesium water clear liquid. Pyrolyzing the heavy magnesium aqueous clear liquid into basic magnesium carbonate precipitates, the precipitates are separated and dehydrated, dried, and crushed to obtain finished products.
The second is the halocarbonization method, that is, bittern is used as raw material, and carbon dioxide, dolomite or lime produced after calcination with dolomite or limestone are used as raw materials, and then digested, precipitated, carbonized, pyrolyzed and other reactions are carried out to obtain light magnesium carbonate.
The third is the brine soda ash method, that is, the bittern is diluted and added to soda ash solution, and after filtration, washing, crushing, drying, crushing, winnowing, packaging and other processes, the finished product of light magnesium carbonate is obtained.
The fourth is the brine bicarbonate method. After the bittern is removed from impurities, it is mixed with ammonium bicarbonate in an appropriate proportion to carry out a precipitation reaction, and then centrifugally dehydrated, dried, and crushed to obtain light magnesium carbonate. At the same time, there is a small amount of magnesium carbonate in the mother liquor. Sodium chloride and ammonium chloride, sodium chloride can be separated after filtration, and ammonium chloride can be recovered by crystallization after evaporation and cooling.
In order to overcome the above problems existing in the prior art, a preparation method of magnesium carbonate is provided, the process cost is low and the process is simple. Include the following steps:
Step 1) adding magnesium sulfate particles to sodium carbonate solution;
step 2) obtaining magnesium carbonate precipitate and sodium sulfate solution after a period of reaction;
step 3) filtering and separating the magnesium carbonate precipitate from the solution;
step 4) using magnesium carbonate Wash with distilled water for 2-4 times, and then dry with a dryer to obtain pure magnesium carbonate, the mass ratio of magnesium sulfate to sodium carbonate is 1:1.
In described step 1), magnesium sulfate is selected food grade magnesium sulfate, and sodium carbonate is selected food grade sodium carbonate. In the step 2), the reaction temperature is normal temperature, and the reaction time is 30-45min. The step 4) drying temperature is 95-KKK°C, and the drying time is 1-1.5h. Described step 4) the magnesium carbonate that makes is food grade magnesium carbonate.
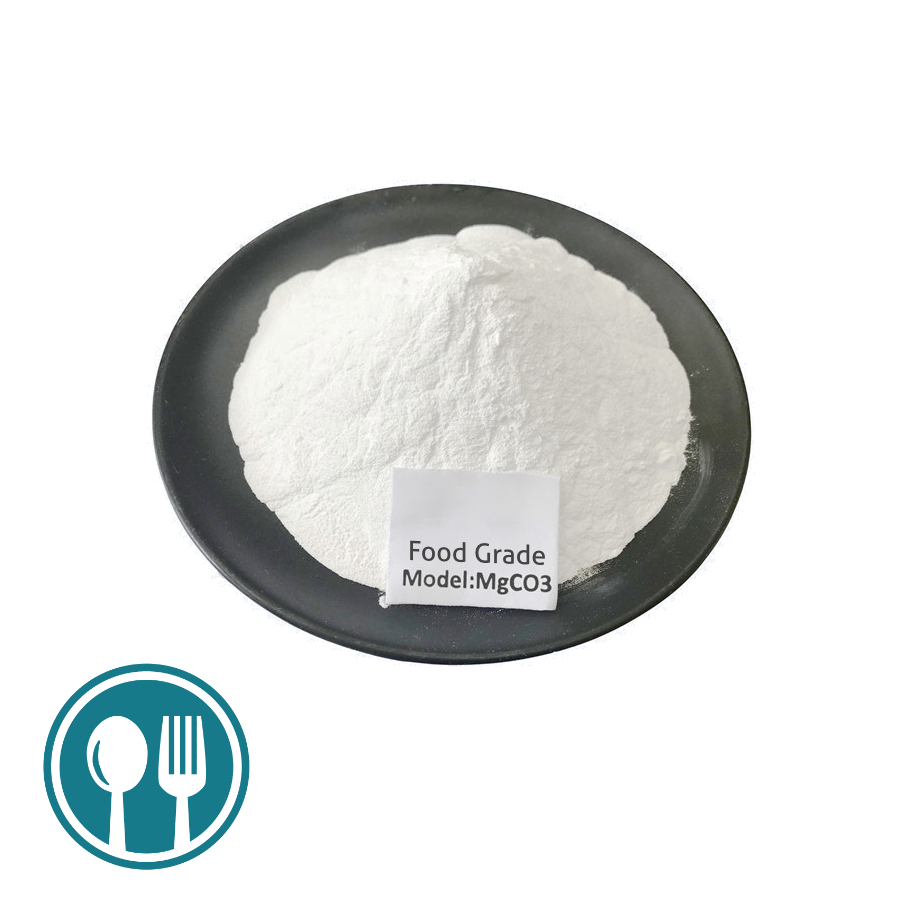
Hebei Messi Biology Co., Ltd. stated that the production process of this kind of magnesium carbonate is simple, easy to control and operate, and the input of raw materials is small, which can greatly reduce the production cost. The produced product is food-grade magnesium carbonate.