Hebei Messi Biology Co., Ltd. stated that nano magnesium oxide is a new type of inorganic functional material, which is widely used in ceramic materials, catalysts, electrical insulation materials, cosmetics, refractory materials, superconducting materials, rubber fillers, acid gas adsorbents, catalysts In fields such as carriers, it can also be used as radar absorbing materials and antibacterial materials. It has broad application prospects and huge economic potential. This paper uses cheap inorganic magnesium salt as raw material and uses hydrothermal method to prepare nano-magnesia powder. The influence of reaction medium on the morphology of nano-magnesia powder is discussed, and the spark plasma sintering (SPS) nano-magnesia powder is systematically studied. The sintering mechanism of bulk solidification was used to test the mechanical properties of solidified nano-magnesia ceramics. At the same time, the catalytic performance of thermal decomposition of ammonium perchlorate (AP) by nano-magnesia powder was systematically analyzed.
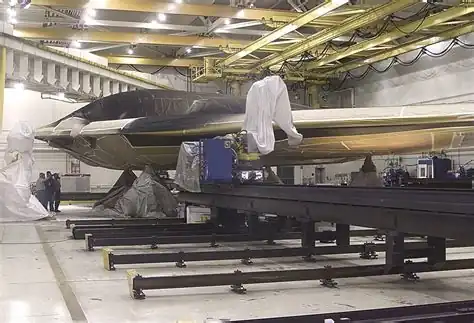
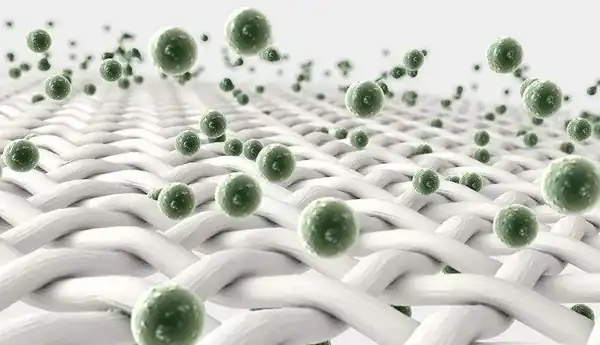
The orthogonal experimental method was used to analyze the influence of process parameters such as the molar ratio of precipitant to Mg2+, hydrothermal reaction time and hydrothermal reaction temperature on the yield, average particle size and morphology of the prepared nano oxide powder, and determined the method for preparing nano oxide powder. The optimal process conditions for oxide powder are: molar ratio of precipitant to Mg2+ 2:1, hydrothermal reaction time 3h and hydrothermal reaction temperature 160°C. The single factor experimental method was used to determine the precipitant and precursor decomposition calcination temperature for preparing nano-magnesium oxide powder.
The effects of disodium ethylenediaminetetraacetate (EDTA) and potassium chloride (KCl) as reaction media on the morphology and structure of nanooxide powders were discussed. After adding EDTA or KCl to the hydrothermal reaction system, the morphology of the nano-magnesium oxide powder gradually changes from hexagonal flakes to nearly circular flakes, and the crystal form is still a face-centered cubic structure. The mechanism of crystal growth was explained using the negative ion coordination polyhedral growth unit theory, and the mechanism of crystal morphology change was discussed.
The spark plasma sintering method was used to study the phase composition and grain morphology characteristics of magnesium oxide bulk ceramic materials sintered at different temperatures (900°C, 1050°C, 1200°C, 1300°C, 1420°C). Sintering temperature has an important influence on grain growth and ceramic structure. XRD results show that the bulk ceramic materials all have a face-centered cubic structure with a single phase composition and high sample purity. After sintering at different temperatures, the diffraction peaks of each crystal plane obviously become sharper and narrower, indicating that grain growth occurs during the sintering process. SEM shows that as the sintering temperature increases, the appearance of the particles gradually evolves from hexagonal flakes to polyhedral morphology, and the gaps between particles gradually transition from continuous pores to isolated pores. The kinetic growth index n value and grain growth activation energy Q value under different sintering temperatures were calculated using phenomenological kinetic theory. Analysis shows that when the temperature is 900℃ and 1050℃, the sintering and grain growth mechanism is mainly surface diffusion; when the temperature is 1200℃, the sintering and grain growth mechanism is mainly surface diffusion, supplemented by plastic flow; temperature When sintering at 1300°C and 1420°C, the sintering and grain growth mechanism is mainly grain boundary diffusion supplemented by plastic flow.
The microhardness of magnesium oxide ceramics sintered at different temperatures and holding times was measured using the Vickers microhardness method, and the bending strength of the ceramic sintered bodies sintered at different temperatures was tested through a three-point bending test. The factors affecting the hardness of ceramics were discussed, and porosity and grain size were considered to be the main factors. From the microstructure morphology of ceramic materials, the main factors affecting the strength of magnesium oxide ceramics were discussed, including grain size, porosity and dislocation density. the size of. The catalytic activity of nano-magnesium oxide powder was evaluated from three aspects: AP’s high-temperature exothermic peak temperature, apparent decomposition heat and low-temperature weight loss rate.
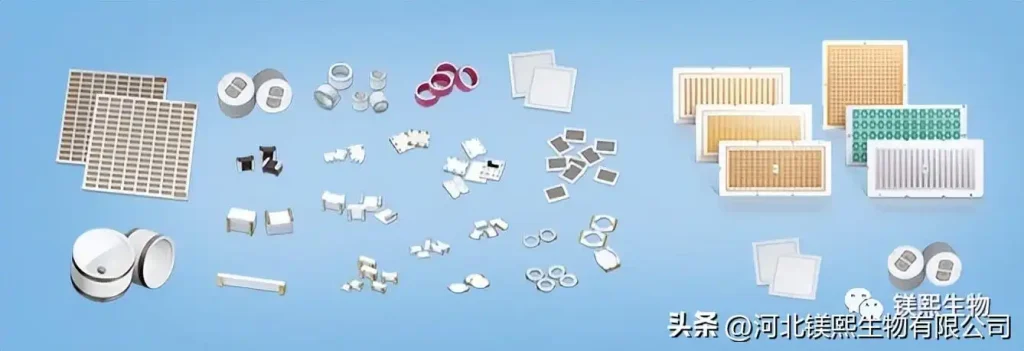
Research shows that nano-magnesium oxide powder shows good catalytic activity for AP, reduces the high-temperature decomposition peak temperature, increases the apparent decomposition heat, and greatly improves the low-temperature decomposition weight loss rate of AP. The kinetic parameters of the AP decomposition process catalyzed by nano-magnesium oxide powder were studied using the Kissinger method. The mechanism of AP catalysis by nano-magnesium oxide powder was studied using electron transfer theory. Studies have shown that the large number of surface hydroxyl groups, low-coordinated hydroxyl groups, H-ions and other active centers existing on the surface of nanocrystals can become traps for capturing electrons and accelerate electron transfer; the small grain size of nanomaterials can improve the unsaturated coordination on the surface of nanomaterials. The number of atoms forms a large number of highly active edges, central defect points and incomplete crystal faces. These surface effects can greatly improve the catalytic performance.